
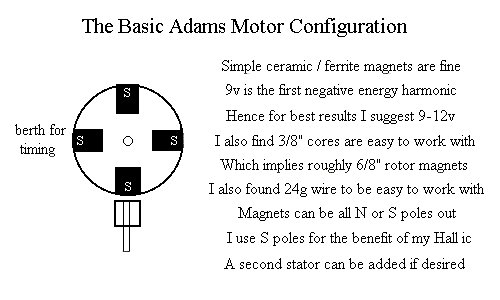
This current is small but valuable and can be harnessed, stored or otherwise utilized. As it collapses a current is produced in the coil (sometimes called “back EMF” – electromotive force). After being energized by a short pulse, the magnetic field formed around the electrical coil then collapses. This repulses the magnet in the rotor, causing it to rotate. The electrical coils are normally wound so that, when energized with a short pulse of current, they produce a repulsive force.
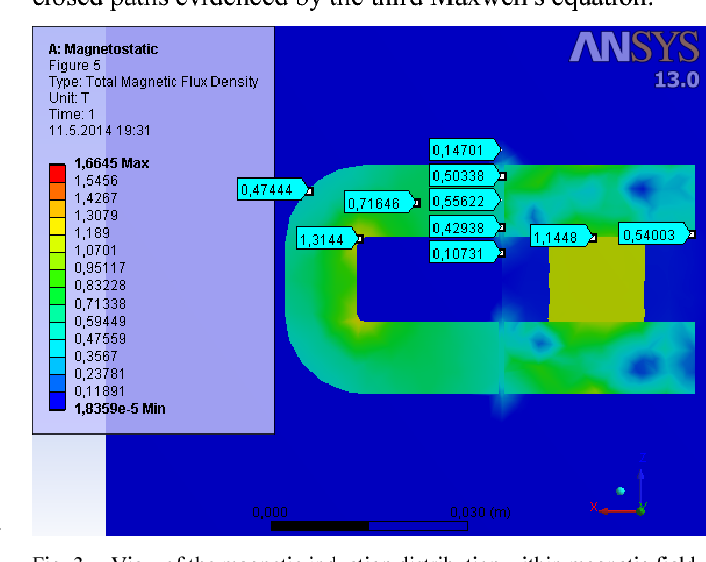
This requires very precise timing, usually achieved through some type of electronic control circuit. The coils are energized when they are exactly lined up with the permanent magnets in the rotor. They are positioned so that the magnets line up with the coils during part of the rotation. The stator is the stationary part of the motor that surrounds the rotor. The example figure at right shows all the magnets facing radially outward. These magnets are usually extremely strong and can be arranged in a variety of different configurations. Typically, it is quite heavy, acting as a flywheel, and has multiple permanent magnets spaced equally around its periphery. The part of the motor that spins is called the rotor. A pulsed motor, unlike normal A/C or D/C types, uses short pulses of current to drive the motor, making it spin.
